Orbital Welding Systems
Thick-Wall Power. Repeatable Welds.
ORBITAL FUSION
Precision Welds for High-Purity, Thin-Wall Applications
At SEC Industrial, we deliver orbital welding systems engineered for accuracy, speed, and repeatable performance. Whether you're welding tube, pipe, or sanitary fittings, our automated solutions eliminate guesswork and help you meet even the most demanding specs - every time.
From portable fusion heads to fully integrated shop systems, our equipment supports a wide range of applications and industries. Each system is designed for clean, consistent welds with minimal distortion and maximum control. You’ll get precise tuning over spot size, gas flow, and output — all from a single console.
We focus on throughput, safety, and system integrity — not just the weld. With built-in automation and real-time monitoring, SEC helps you scale production while maintaining the highest standards of quality.
Looking for the right tool for the job? Let’s talk orbital welding systems that perform under pressure — and deliver when precision matters most.
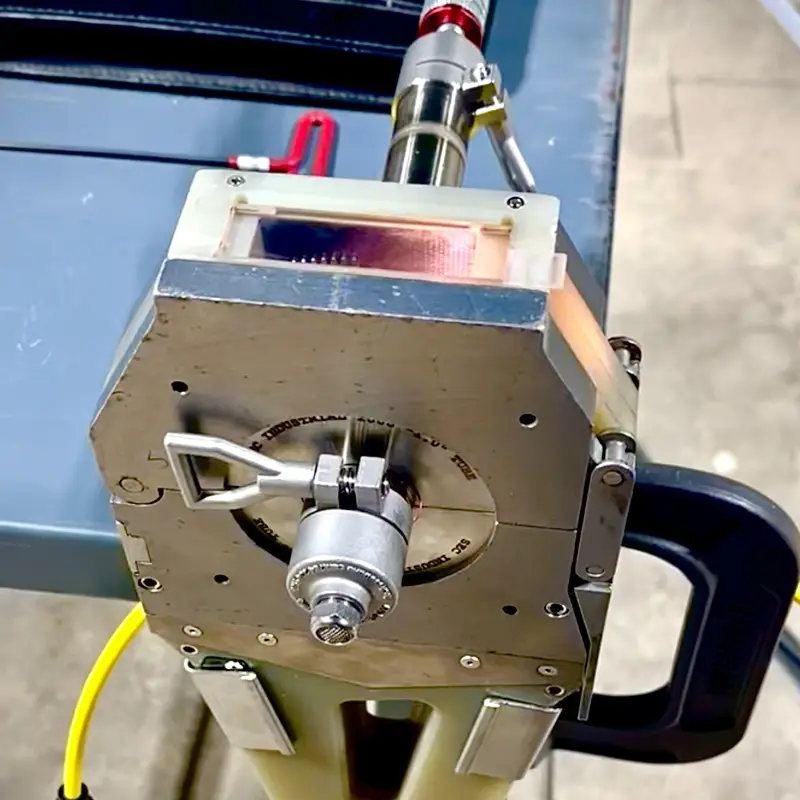
Precision Control
Dial in spot size, gas flow, and output with exact parameters — all from a single console.
Automated Consistency
Advanced monitoring ensures repeatable welds with minimal distortion and no material waste.
Fast Travel, Clean Results
Achieve high-speed welds without compromising quality
Orbital Fusion Equipment We Offer
SEC is a proud supplier of custom-engineered orbital fusion welding products that offer the highest weld quality and consistency.
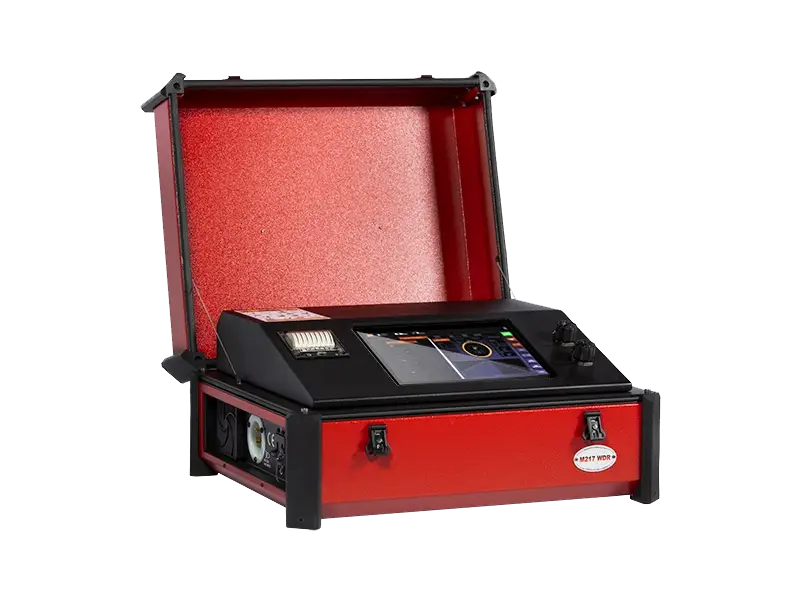
Model 217 Power Supply
The Model 217 WDR is a 100/150A programmable GTAW power supply designed to work with all AMI’s orbital fusion weld heads. This device is capable of welding tubes and thin-wall pipes.
The Model 217 power supply produces welds that successfully meet or exceed the required specifications of various industries. These fields include semiconductor, bio and pharmaceutical, aerospace, food, dairy, beverage, renewable energy, and nuclear. Request a quote below with us today.
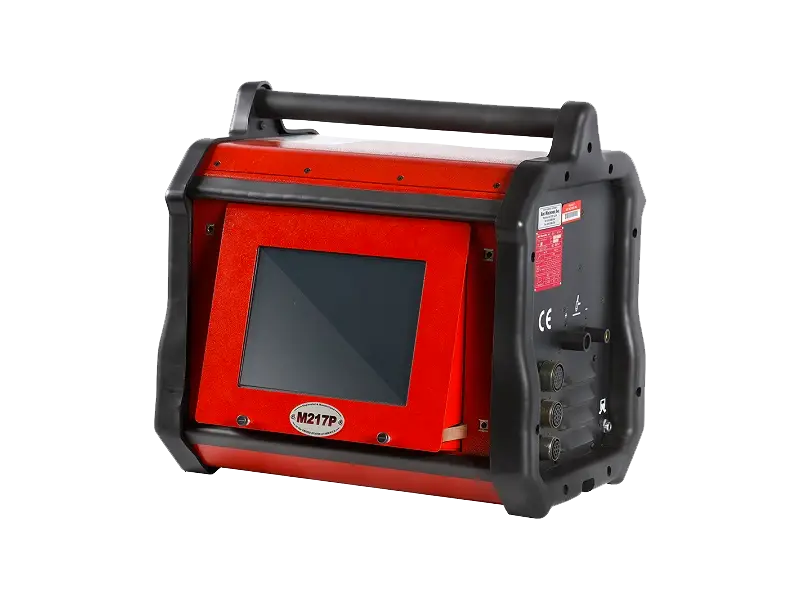
Model 217P Power Supply
The Model 217P WDR is the most advanced, easy to use orbital (GTAW) power supply in the industry—capable of welding tube, thin-wall pipe, and fittings from 3/32” (2,3 mm) through7.5” (190,5 mm) OD, in wall thicknesses up to 0.160” (4 mm).
The Model 217P power supply addresses the versatile needs of a wide range of industries. These sectors include semiconductor, food, dairy, beverage, bio and pharmaceutical, aerospace, energy, and other OEM applications. Request a quote for this ultra-portable and feature-rich equipment today.
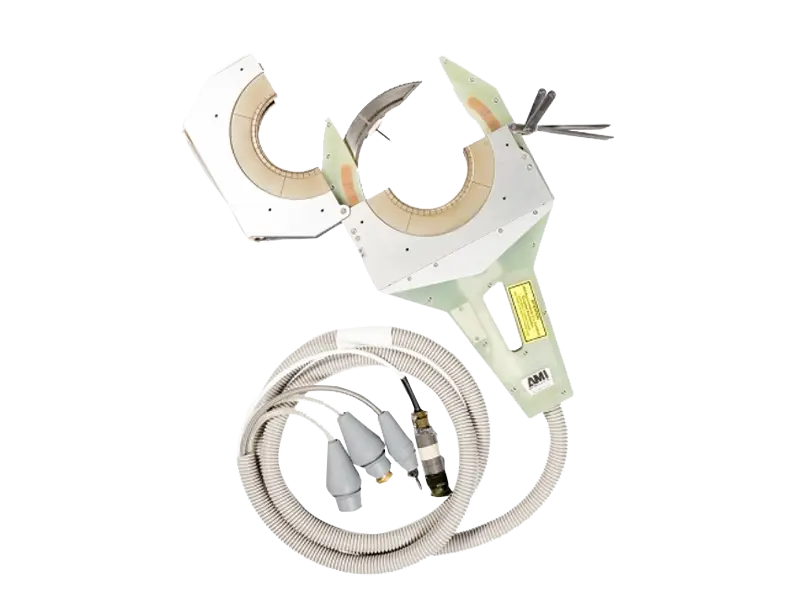
Model 8 Series Weld Heads
The Model 8 series orbital weld heads are designed for fusion (TIG) welding of tube, thin-wall pipe, and fittings through the range of 0.25 in. (6 mm) to 6.625in. (168 mm) OD (outside diameter) and wall thicknesses up to 0.160in. (4 mm). The narrow width of these heads makes them ideal for fitting-to-fitting welds and other limited-clearance applications.
The Model 8 series weld heads incorporate a two-sided clamping mechanism – precision machined and designed to compensate for significant diameter variances while ensuring positive clamping force and concentricity. The insert sizes accommodate an extensive range of applications, and all Model 8 series weld heads are fitted with water-cooling capability – for heavy wall material welding and/or high duty-cycle requirements.
- Fitting support mandrel – to facilitate the welding of short sanitary ferrules without pre-tacking
- Bench mount bracket – to provide secure support when not in use or when bench welding
- Clamp inserts – available in imperial and metric sizes, as well as non-standard sizes for custom applications
- Extension cables – available in 25 ft. (7.6 m), 50 ft. (15.2 m), and 75 ft. (22.8 m) lengths
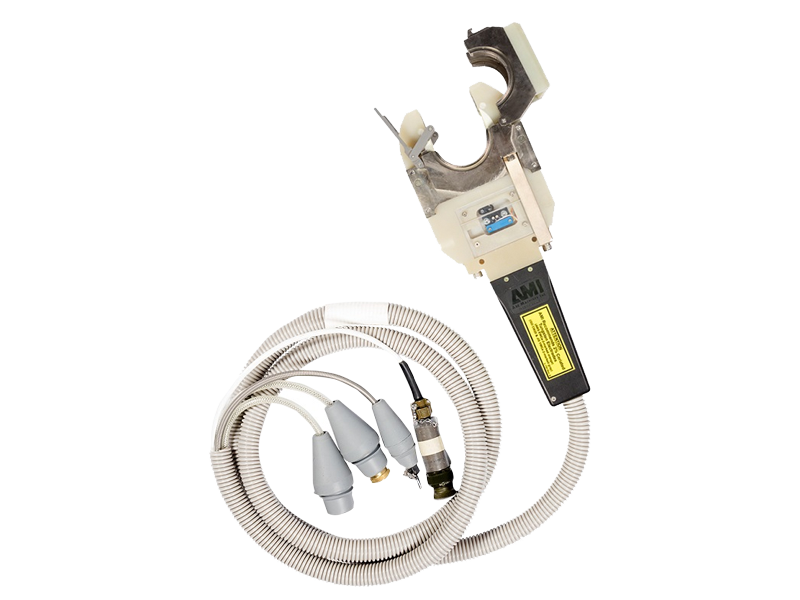
Model 9 Series Weld Heads
The Model 9 series of orbital weld heads are designed for fusion (TIG) welding of tube, pipe, fittings, or other cylindrical components. Available in eight sizes and three versions, they accommodate diameters from 3/32in. (2.3 mm) to 7.5 in. (190.5 mm) OD, and wall thicknesses from 0.01in. (0.25 mm) to 0.16in. (4 mm). Each weld head fits a wide range of tube sizes via easily replaced, size-specific clamps. These weld heads are compatible with all AMI Power Supplies.
The standard Model 9 incorporates a two-sided clamping mechanism to hold components being welded in line concentrically, minimizing the need for tack welding. Several of these heads incorporate a flip-up viewing window, for easy verification of fit-up. Most Model 9 weld heads are plumbed for water cooling of both the cables and internal weld head components – allowing increased duty-cycles.
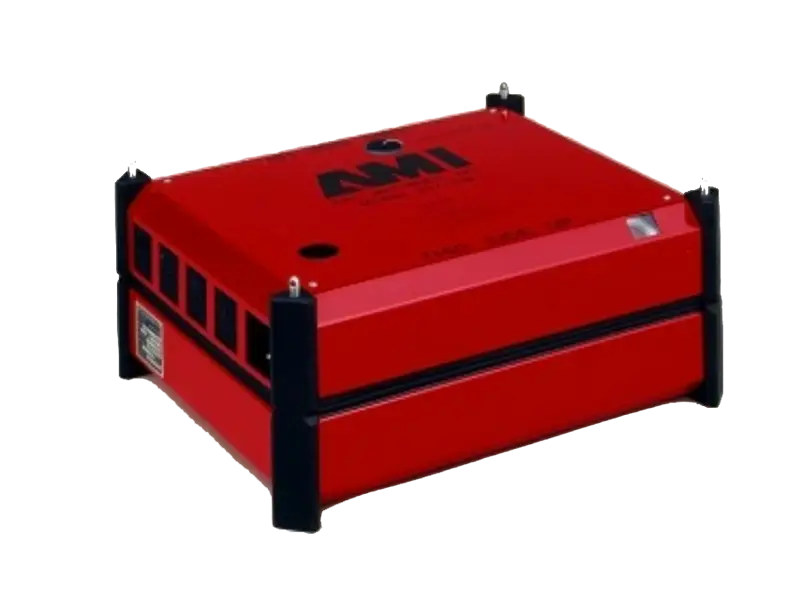
Cooling Units - Fusion
Water-cooled weld heads hold numerous advantages for orbital welding systems on the modern market. Featuring a heavy-duty pump and a flow sensor, these weld head cooling units from AMI attach to the base of the Power Supply. Powered by an outlet in the mating power supply, this configuration provides a recirculating coolant source. Look no further for a reliable cooling unit designed for heavy-wall tube/pipe and/or high-duty cycle welding.
SEC has weld head cooling units available for your specialized applications. Reach out to us today with any questions about specifications, quotes, or compatible products. Our team will provide the knowledgeable expertise you need to help you select the most suitable equipment in the industry.
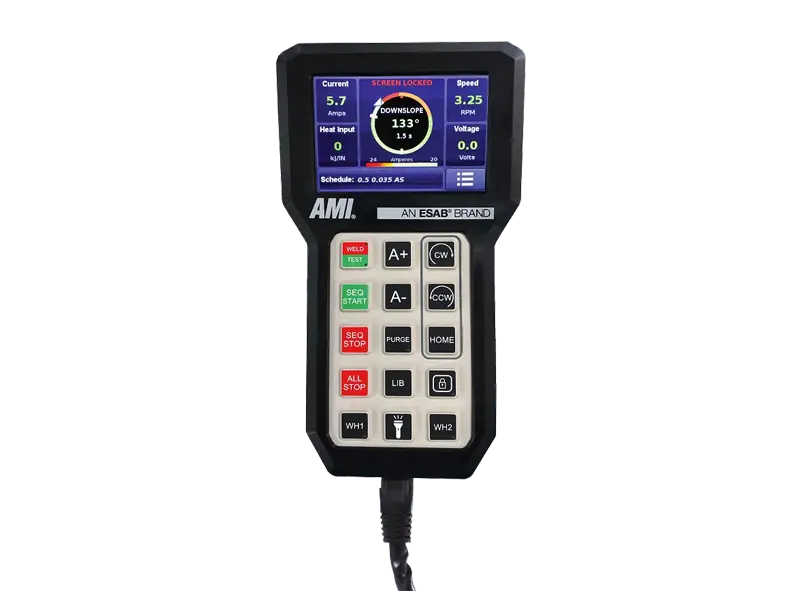
Remote Pendant – Fusion
Remote welding pendants (RP) allow complete control of all welding functions before, during, and after the actual weld cycle. Use the remote welding pendant to make any changes to the welding program before beginning a cycle if needed. Start the weld work location—not the power supply. Monitor the weld cycle and at any time during the weld if needed. Depending on the system being used, you can also change your weld programs, data requirements, etc., from the RP. Uncover more about these high-quality RPs available at SEC below.
- Touch Screen Graphical Display
- Select from the library of weld schedules
- Compatible with the M217 & M217P Weld System Controllers
- Operates the “New” Dual Weld head Controller
- Integrated Flashlight
ORBITAL PIPE
Heavy-Duty Solutions for Pipe Welding at Scale
At SEC Automation, we deliver orbital welding systems engineered for accuracy, speed, and repeatable performance. Whether you're welding tube, pipe, or sanitary fittings, our automated solutions eliminate guesswork and help you meet even the most demanding specs - every time.
From portable fusion heads to fully integrated shop systems, our equipment supports a wide range of applications and industries. Each system is designed for clean, consistent welds with minimal distortion and maximum control.
We focus on throughput, safety, and system integrity — not just the weld. With built-in automation and real-time monitoring, SEC helps you scale production while maintaining the highest standards of quality.
Looking for the right tool for the job? Let’s talk orbital welding systems that perform under pressure — and deliver when precision matters most.
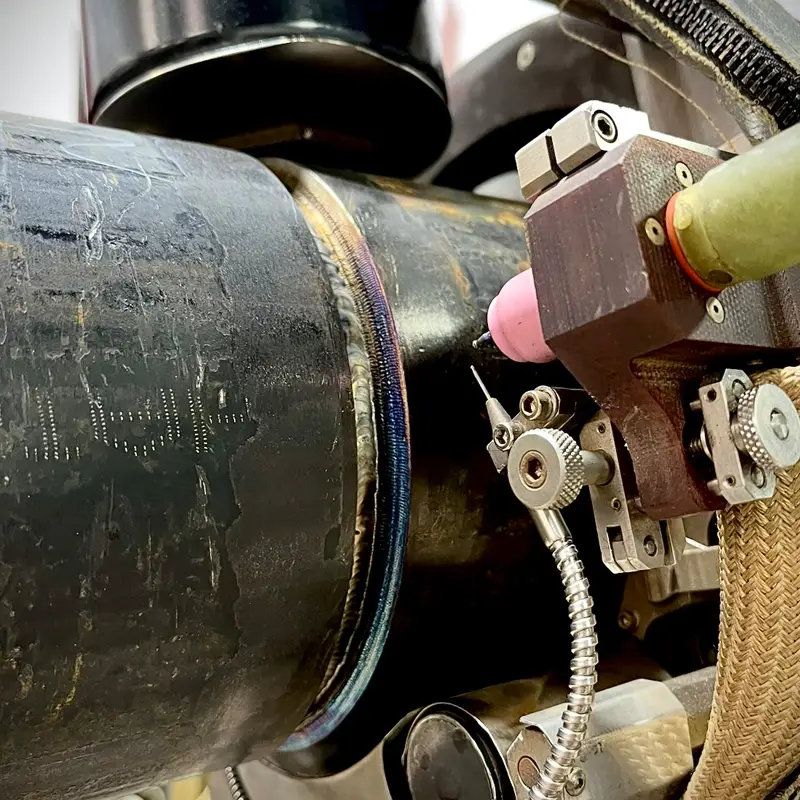
Precision Control
Dial in every aspect of the weld parameters.
Automated Consistency
Advanced monitoring ensures repeatable welds with minimal distortion and no material waste.
Fast Travel, Clean Results
Achieve high-speed welds without compromising quality
Orbital Pipe Welding Equipment We Offer
SEC is a proud supplier of custom-engineered orbital welding products that offer the highest weld quality and consistency.
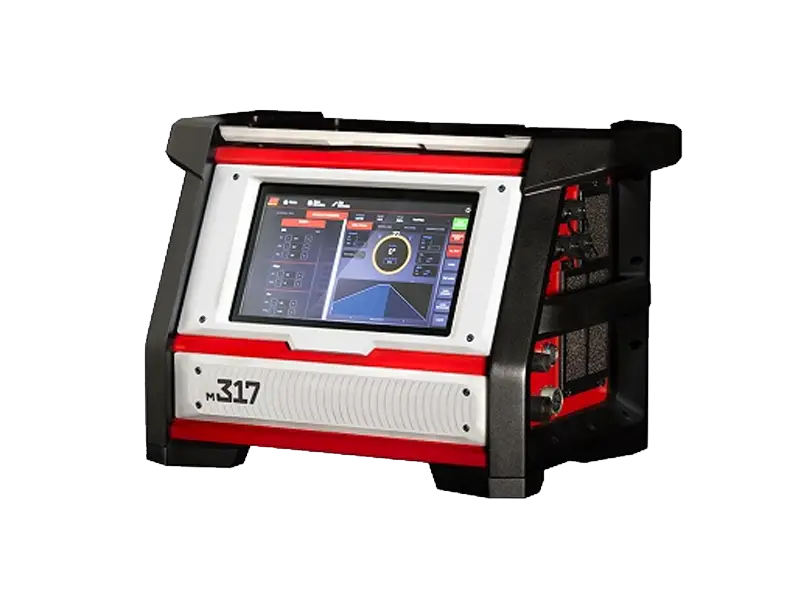
Model 317 Power Supply
Orbital Welding Controller Experience the next generation in orbital welding technology. Designed for welders by welders. At AMI we provide 40 years of automated welding expertise with the most modern controls and interface technology. Multiple security levels allow for control of weld schedule, and change limits within prescribed limits. Unrivaled user interface.
- With 100% Duty cycle, the Model 317 provides the highest power/weight ratio in the industry
- Unrivaled user experience: modern touchscreen improves performance and increases production efficiency
- Advanced Orbital welding features
- Vision system enabled
- Weldcloud and orbital analytics: Collect, store and mange your data files locally or on the cloud
- Advanced orbital analytics to maximize performance
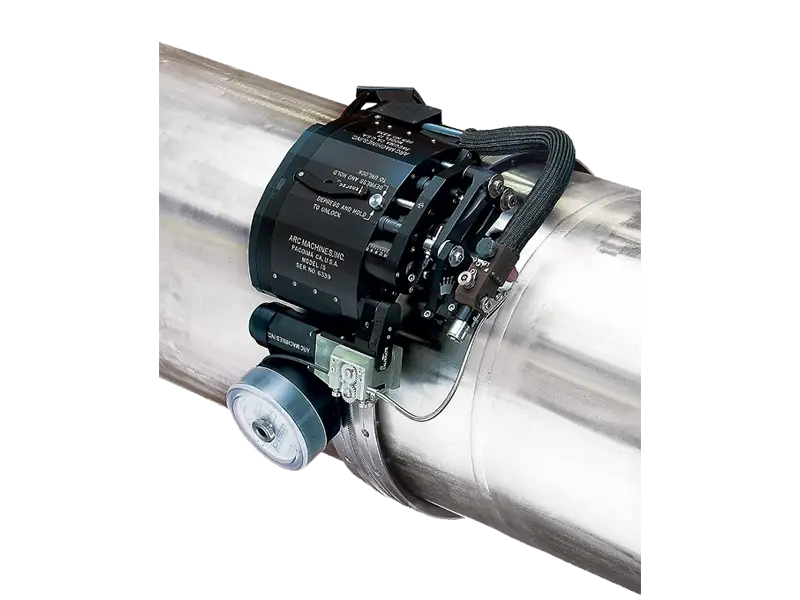
Model 15 Weld Head
The Model 15 weld head is a rugged, precision weld head with low radial clearance for GTAW welding of all pipe sizes from 3″ (76 mm) pipe up to an unlimited size, including flat plate. With a large diameter, it’s primarily designed for field use in the nuclear, shipbuilding, petrochemical, and construction industries where exceptional weld quality is strictly required.
The Model 15 weld head features rotation, wire feed, automatic voltage control, cross-seam steering, and torch oscillation. It is available in many standard configurations and can be retro-fitted or customized with numerous application-specific accessories to accommodate every need. The Model 15 is just one element of an automated pipe welding system. A torch assembly, precision guide rings, AMI Power Supply, and other options comprise a complete system suitable for high-quality orbital pipe welding. Reach out to the SEC team with any questions today.
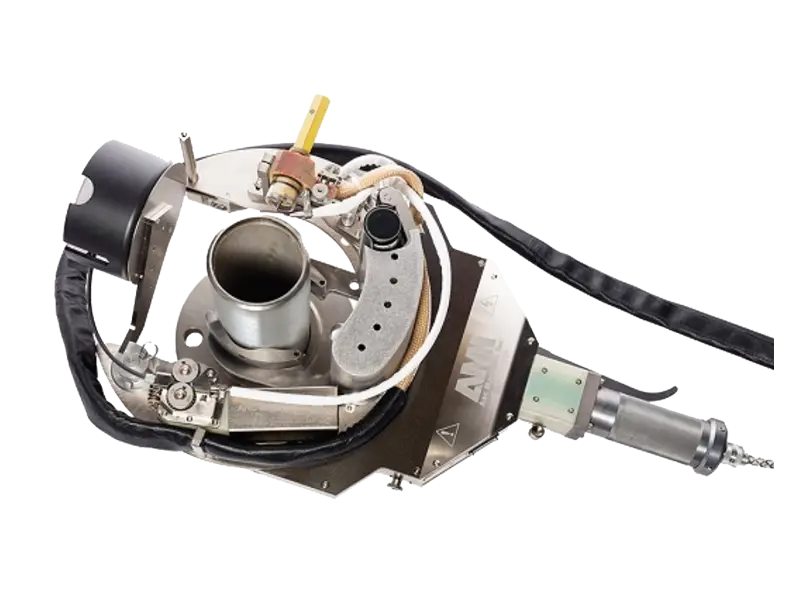
Model 79 Series Weld Heads
The high-durability Model 79 series weld heads are designed for fabrication shop and field process pipe welding applications. Model 79 series weld heads have a unique integral clamping system which gives each weld head the ability to adjust for different pipe and tubing diameters in seconds, thereby eliminating the requirement for specifically sized guide rings.
Perfect for specialty utilization, the full-function M79 weld head series can accommodate a range of pipe sizes from 0.75 in. OD to 6.625 in. OD (19 mm to 170 mm) and wall thicknesses up to 0.75 in. (19 mm). Contact the team at SEC Industrial with any technical-specific questions or to request a quote today.
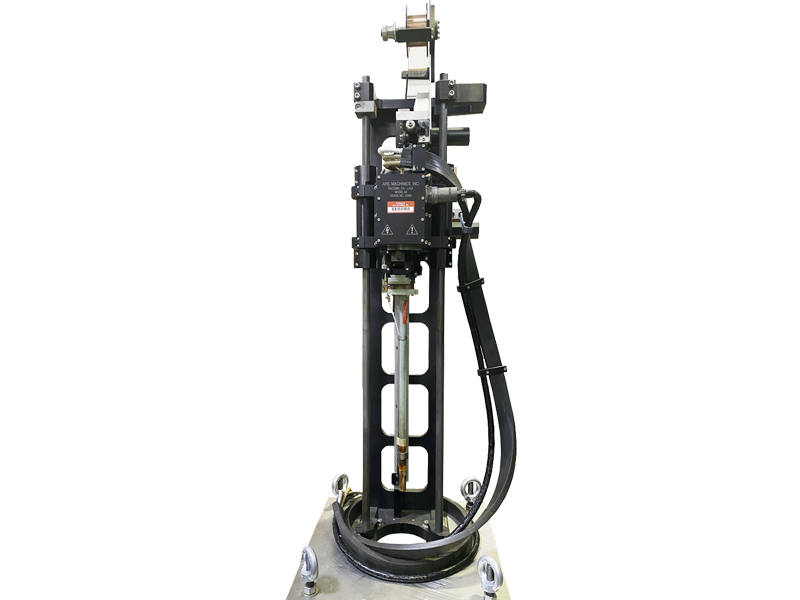
Model 94 Spiral Cladding Pipe Weld Head
The Model 94 is a rugged weld head designed for high production spiral or step ID cladding and groove welding on small diameter pipes, fittings, and vessel inlet/outlets, using the GTAW (TIG) process with cold wire feed. The M94 is a stable, precise, and repeatable platform for manipulating many different torches for welding and cladding operations.
The Model 94 uses accessories to accurately position the weld head in axial alignment with the part to be clad. A manual travel clutch allows fast insertion and extraction of the torch, and axial readout gives precise torch location. The use of commutators in the M94 allows continuous torch rotation. The Model 94 ID spiral cladding pipe weld head is self-supporting on the work piece and can operate in any position.
- In-place ID cladding of nozzles
- Servo-controlled: AVC, Rotation and Axial Travel, Wire Feed
- Axial position readout
- Stainless steel rack-and-gear drive for consistent travel speeds in all positions (no friction drives)
- Manual travel clutch to allow rapid insertion and extraction of torch
- Pulsed current welding, and synchronized pulsed-wire feed
- Unlimited torch rotation (no cable wrapping)
Continuous spiral cladding capability (depending on application) - Pre-set function for H.F. starts
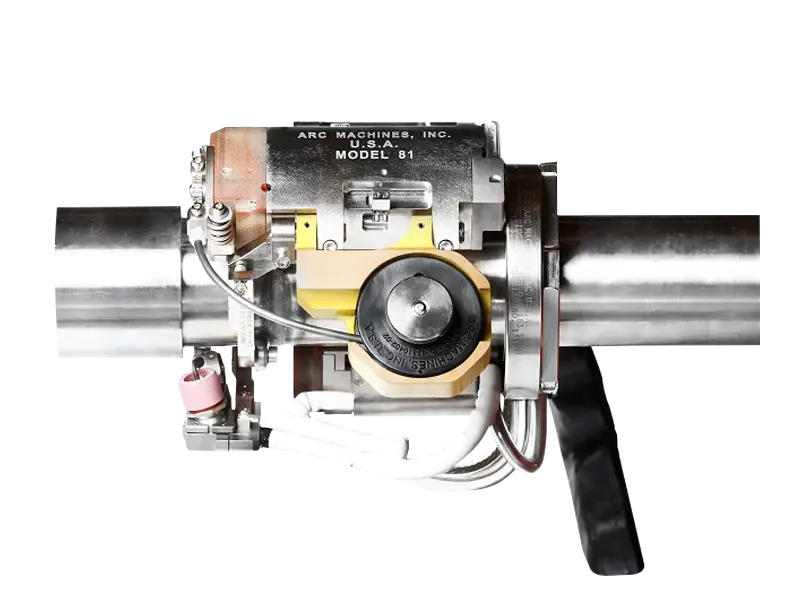
Model 81 Small Pipe Weld Heads
The Model 81 is a full-function orbital pipe weld head featuring programmable Arc Voltage Control, Torch Oscillation, and onboard Wire Feeder and Travel in a very compact package.
The Model 81 in its standard configuration will weld pipe from 1.9 in. (48 mm) OD to 5.563in. (142 mm) OD with as little as 1.750in. (45 mm) radial clearance and 6.325in. (161 mm) axial clearance.
The Model 81 is employable in utilizations that require high-quality welding results in applications with limited axial and radial clearances. Common uses for the Model 81 include shipbuilding and high-pressure steam piping in fossil fuel power plants and many other applications.
The unique clamping assembly of the Model 81 small pipe weld heads increases production rates by minimizing the mounting and dismounting times of the weld head to as little as 30 seconds each.
- Servo-controlled: Rotation, AVC, Synchronized Wire Feed, Torch Oscillation
- Motorized torch steering
- Water-cooled body for use in pre-heated pipes
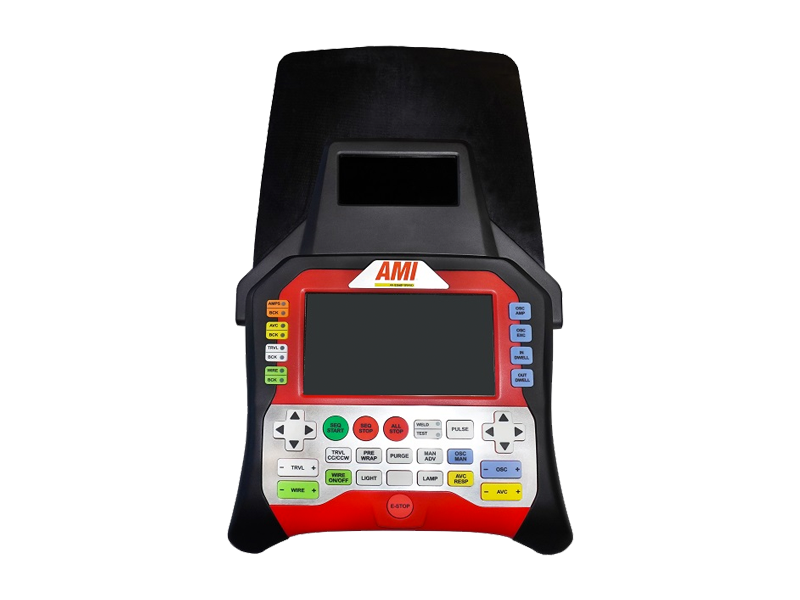
Remote Pendant – Pipe
Welding control units—also known as remote pendants (RP)—grant users complete control of welding operations. With remote pendant technology, welding operators no longer have to settle for less-than-ideal settings or conditions during a cycle. Welders have the significant ability to set parameters remotely to increase user safety and boost arc-on time. Improved productivity is yours with a heightened level of weld position and placement flexibility.
SEC Industrial offers a remote pendant for our customers’ ongoing fabrication and fieldwork, including pipe welding functions. The key features of this industrial remote control include its ergonomically engineered design, operator safety protection, user-friendly keypad and touch screen operation system, convenient viewing lenses, and the ability to select, adjust, override, or halt weld programs. Reach out to our team to learn more about this specialty product or request a quote today.
- Remote control of all welding functions for pipe
- Ergonomic design
- Combination of Touch Screen and Keypad entry and operation
- Ability to select weld programs
- Ability to execute, adjust, override, and stop weld programs
- User-Friendly graphic user interface (applies only to M317 pendant)
- Keypad includes a color reference for similar weld functions
- Includes operator arc protection (removable/replaceable) with weld viewing lens